The small steel ball is inconspicuous, but its role is extremely extensive. In industrial machinery, it is an indispensable part of bearing parts; in sports, it can be used as a filler for catapults; and in laboratory equipment, it is an important part of accurate measurement tools. Whether it is a high-strength corrosion-resistant steel ball used in the aerospace field or a standard specification model in golf course practice equipment, these steel balls silently play an important role on their respective stages.
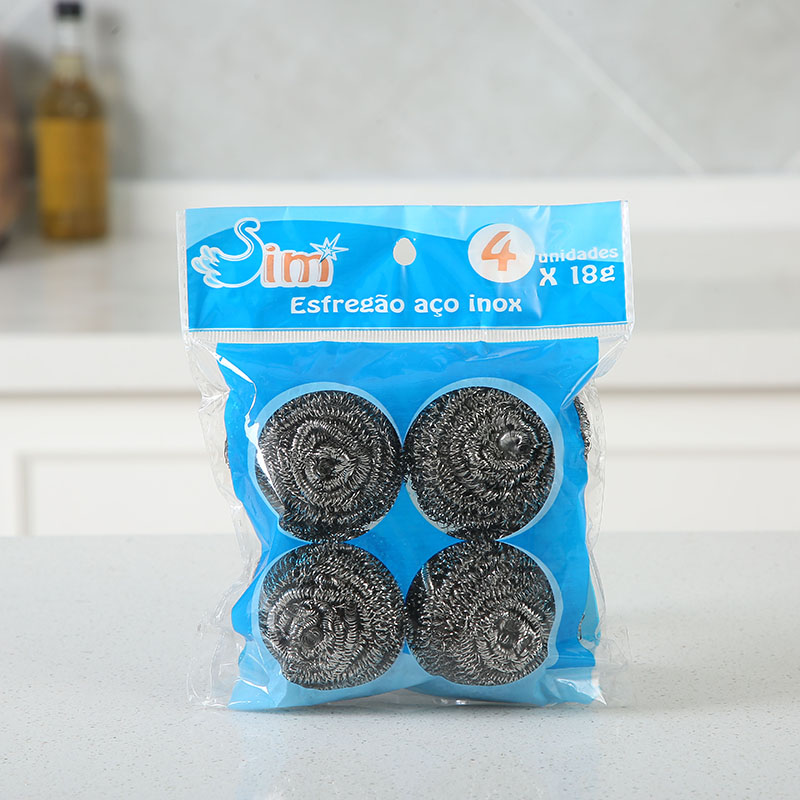
A good steel ball is inseparable from high-quality materials and exquisite craftsmanship. To judge whether a steel ball is qualified, we need to consider a number of factors: first, the purity of the material, pure metal composition can effectively reduce friction loss; second, the surface smoothness, higher smoothness can reduce the energy loss during operation; the second is the hardness value range, the appropriate hardness can not only extend the service life, but also better withstand the test under various pressure conditions. Compared with ordinary carbon steel, the steel ball after special alloy treatment shows more superior performance, especially suitable for long-term stable work in high-load operating environment.
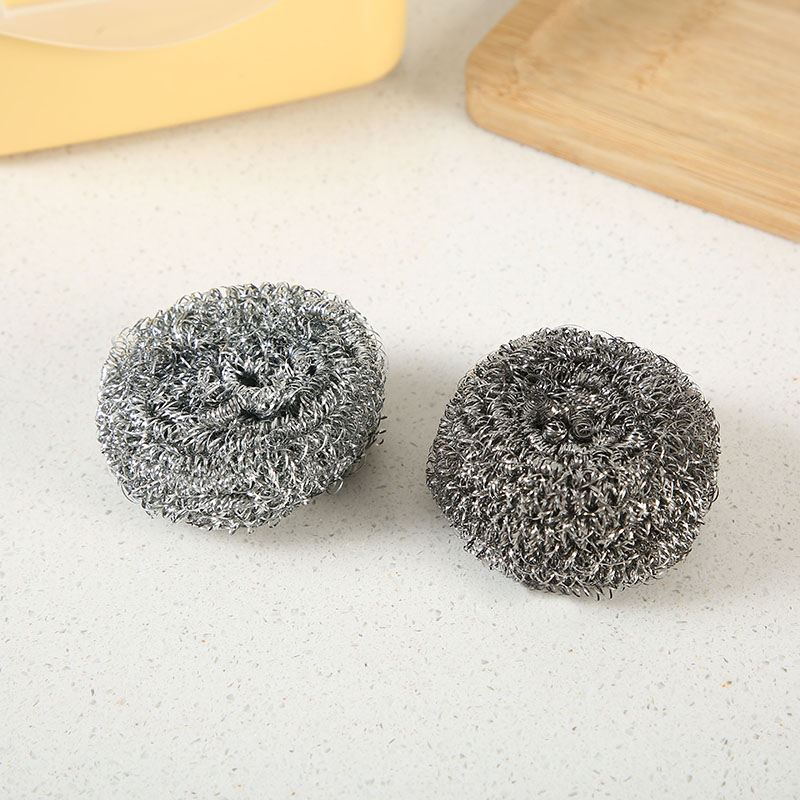
Behind the excellent steel ball often stands a group of technicians who strive for perfection. Take some leading international manufacturers as an example. They have greatly improved their efficiency by introducing highly automated production lines, supplemented by human sampling to ensure zero defects in product quality. Every link is strictly controlled, from raw material screening to finished product packaging in accordance with the highest standards. This dual gatekeeping mechanism not only enhances the trust of customers, but also sets a new benchmark for the development of the industry.
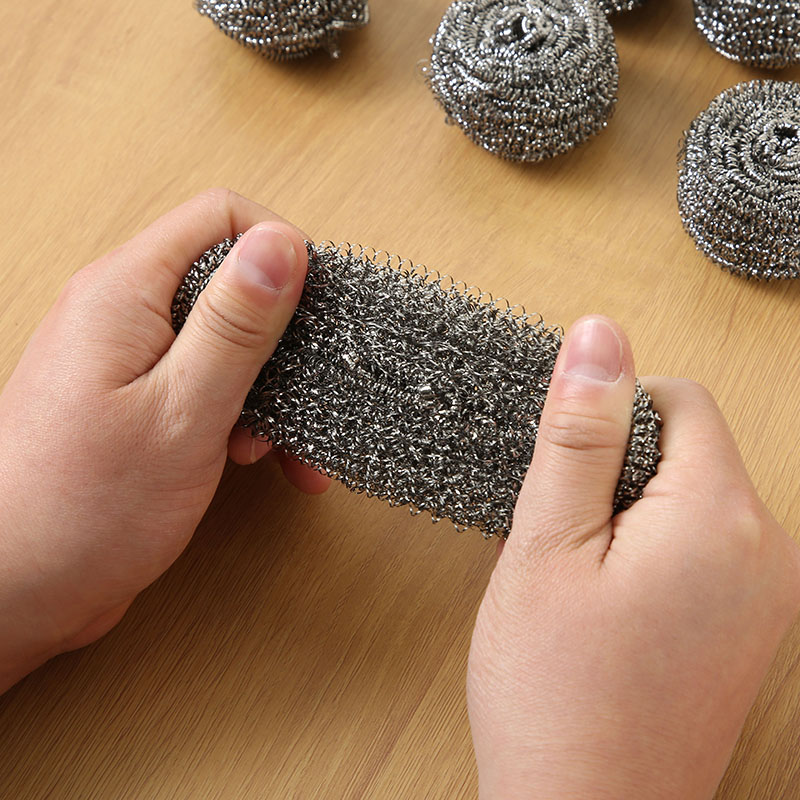
With the advancement of technology, the future steel ball may develop in the direction of more functionality. For example, the "self-lubricating" feature under development will enable steel balls to operate smoothly without additional lubricating oil, a breakthrough that is expected to greatly simplify the maintenance process of mechanical equipment and reduce costs. In addition, intelligent monitoring methods may also be integrated into the new generation of products, allowing real-time monitoring of status data to detect problems in time and take measures to prevent failures. These new technologies will certainly promote the whole industry to a higher level of development stage.
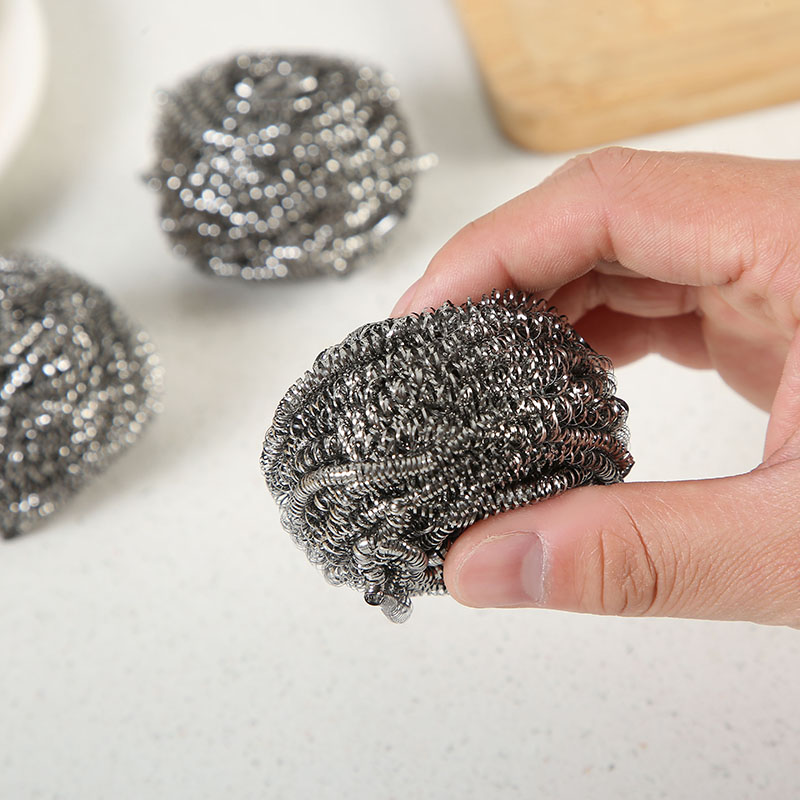
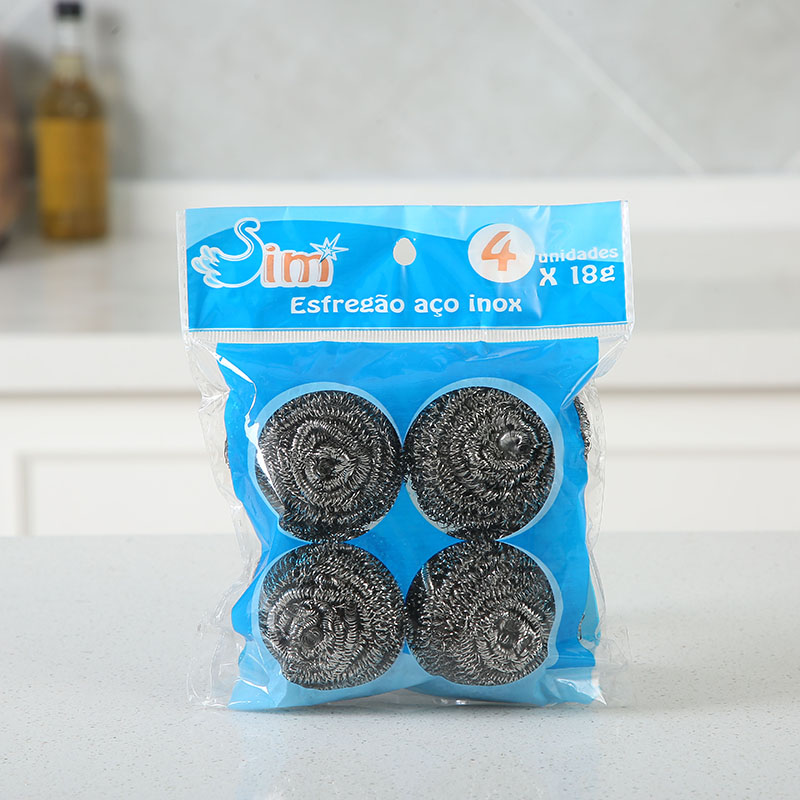